
The Dynatest Runway Friction Tester is fully integrated to a vehicle with all required equipment and a water tank for maintenance and compliance testing. All Dynatest friction data can be imported to its Airports Pavement Management System, which goes a stage further and consolidates many different parameters to provide optimised maintenance regimes.
Ingenuity and innovation are words that resonate throughout the airport industry, where concepts beyond imagining are entering into every aspect of the passenger and airfield process – the very incarnation of ‘state-of-the-art’. At airside, cutting-edge, intelligent technologies are enhancing operational safety at airports worldwide, and with environmental efficiency and economical expenditure so high on airport agendas, employing the optimum solutions in runway friction testing, ground lighting and wildlife dispersal is more important now than ever.
“The single greatest asset an airport has is its runway. Timely maintenance activities save time and money and minimise disruption,” said David Leask, Vice President Business Development of Dynatest, specialist manufacturer of friction and other compliance testing equipment. “Runways and taxiways are designed to allow the safe operation of aircraft in all operating conditions, including emergency situations. Key to this is the contact point between the aircraft and the runway and this is where friction is critical.”
Next generation friction testing
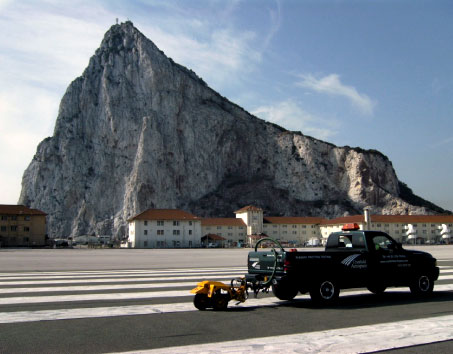
As an unbiased, independent surveyor, Cranfield Aerospace is in a unique position to provide runway friction classifications and monitoring surveys on an ad-hoc or frequent basis. All of its surveys are carried out in line with UK CAA CAP683, ICAO Annex 14 or MADS standards.
Factors such as adverse weather, surface materials and wear act as contaminants that serve to reduce a runway’s available friction, which left untreated could result in aircraft not being able to safely perform manoeuvres, emergency or routine. It is for this reason that the utilisation of state-of-the-art, new generation technologies that examine runway conditions is high-ranking in airports’ list of priorities.
The fully integrated Dynatest Runway Friction Tester works on the ‘fixed slip’ principle, with a hydraulically braked measuring wheel operating at 14% slip to identify the effect of contaminants, allowing the necessary maintenance actions to be put in place. “Dynatest is leading in the integration of its friction testers with GPS and third party data that enables accurate and timely dissemination of contaminant locations during adverse weather, with enhanced awareness of changing airfield surface conditions,” Leask added. “This results not only in the quicker treatment of critical areas but a saving in the associated costs, and, through the optimised placing and use of chemical de-icers, a reduced environmental impact at the airport.”
By knowing accurately the position and extent of runway contaminants, maintenance can be applied in the correct location saving the airport time, enhancing traffic with reduced runway closures, and limiting expense. “The implications of an incident due to poor runway friction would do much more damage to an airport’s reputation than it would to its infrastructure. A runway can be resurfaced, but reputation takes years to rebuild,” added Paul Keating, Project Manager and Trials Engineer for independent Runway Friction Surveyor Cranfield Aerospace. Utilising cutting-edge Douglas Mu-Meter technology and a custom modified tow vehicle, Cranfield Aerospace is deftly suited to annual or interim runway classifications, surveys following runway resurfacing or maintenance programmes, and for specialist investigations, such as the study of new materials or post accident investigations.
“All our surveys provide friction contour maps of the runway that can be used to highlight specific areas where the friction properties may not meet the requirements of the applicable standards,” Keating explained. “Detailed friction contour mapping allows airports to see individual areas of concern as they begin to arise. This may mean that only small areas of runway need maintenance, rather than fully resurfacing a whole runway. On the other hand, a friction survey may prove that a runway is operating better than expected, meaning that no additional work is required.”
Runway friction testing provides evidence, as well as reassurance, that an airfield’s runway is in good health and still meets the friction requirements set out by governing bodies. Regular monitoring can also be used to highlight areas of concern on the runway and notify operators when their runway is dropping in performance, thus allowing airports time to react long before it becomes unsafe.
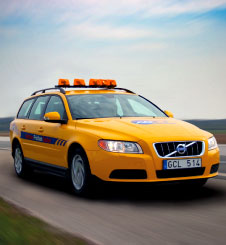
ASFT systems are making a difference daily at airports and on roads all over the world. Its friction testers are making airports safer to operate, and its Early Ice Warning System, combined with RWIS, is making them 30% more efficient, which translates into 30% less cost and 30% more environmental efficiency.
Frederik Graflind, General Manager, ASFT, said: “The most important benefit of runway friction testing is that it can prevent overruns, which in the best case result in high costs and in the worst case, casualties. Having reliable and reproducible measuring results is of utmost importance, as airport operators need to be sure that the information they are receiving and using in their daily work is accurate.” ASFT, a world leading developer and manufacturer of Continuous Friction Measuring Equipment, Runway Weather Information Systems (RWIS), and Early Ice Warning Systems, has one of the most reliable reproducibility records in the friction testing industry. Boasting solutions that are at the forefront of innovation, it has developed unique sensors that identify runway conditions in potentially hazardous weather. The Frensor® freezing point sensor needs no calibration and works on any type of deicing and composition, while OpticEye® is the only precipitation sensor that can detect and classify very fine rain. “ASFT systems are making a daily difference at airports all over the world. Its friction testers are making airports safer to operate, while its Early Ice Warning System combined with RWIS is making them 30% more efficient, which is translated into 30% less cost and 30% more environmental efficiency,” Graflind said.
Long-term planning
As well as the threat of compromised runway surfaces, airports face an array of challenges to airside safety, including the incursion of hazardous wildlife. The newest technology in bioacoustics has for many years been used to disperse birds, and mitigate the ever-present risk of bird strike. “The basic theory remains the same today as it did some 20 years ago when the first system was produced. Since then technology has enabled the broadcast to be much improved, with the quality of both recording and playback becoming as close to the real thing as possible; this enhances the end result, with appropriate specie dispersal,” said David Randell, Director of Scarecrow Bio-Acoustic Systems.
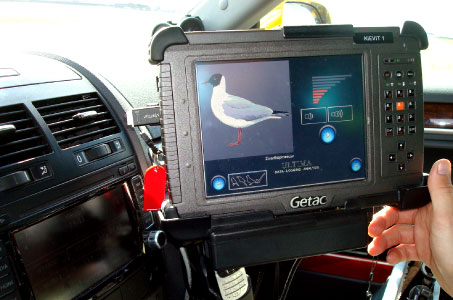
Scarecrow Bio-Acoustic Systems’ Ultima model combines bird dispersal with a full data logging and reporting software system, saving a considerable amount of time in both data collection and data analysis thus providing efficiencies. Scarecrow supplies systems to airports across the globe, and is currently in discussion with airports in Brazil, Columbia, Pakistan, Europe, Australia, New Zealand, Nigeria and the US.
One of the industry’s most major developments was the launch of Scarecrow Bio-Acoustic Systems’ Ultima Bird Dispersal and Reporting software, which then provided the first fully-integrated bird dispersal and data logging system, to incorporate reporting software. Now this system uses a vehicle mounted PC tablet with touch screen technology for ease of use, and most recently, Scarecrow Bio-Acoustic Systems has developed the Threshold Risk Management Module, designed to aid management and save time by using an ‘at a glance’ traffic light system for evaluating the level of risk from the data collected by field operatives, per specie, against pre-determined and user configurable threshold levels. “It will provide information to enable management to focus on the priority issues first, and its user configurable input can be amended at any time to enable the airport management to strive for continuous improvement,” Randell commented.
Substantial weight is accorded, by airports and suppliers alike, to the use of safety solutions that enable ongoing operational improvement while also allowing for continuous profitability. “Airports face many challenges today, of which the most important is to stay profitable long-term. Operationally the major challenges emanate from how to sustain and in the long-term increase existing capacity not only under ideal conditions but for virtually all operational conditions,” explained Ola Håkansson, Director – New Technologies at airport safety solutions specialist Safegate Group. “In order to fully leverage existing and future potential the airport will have to look beyond individual systems, processes and organisational borders. The level of integration will increase but most importantly focus will have to shift from systems and technology to the processes involved in handling the traffic and the passenger flow through the airport.”
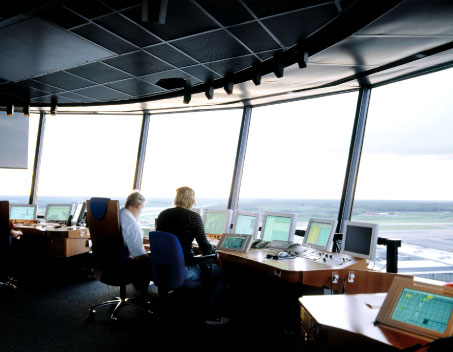
Having worked with more than 1,000 airports in over 100 countries, Safegate Group provides, among other things, control systems for ATC. Since all of its systems are available in-house, Safegate Group can support a higher level of integration and most importantly supply its users with support on an operational level rather than the traditional technical level.
Safegate Group specialises in providing an array of solutions that support increased efficiency and safety, combining operational knowledge and understanding with state-of-the–art-technology and systems reaching from the airfield all the way to the tower and the gates. “Each airport is unique in terms of infrastructure, operational procedures and ambition. In order to support the individual airport to the best of our abilities Safegate Group strives to understand the relevant circumstances at the airport in question,” Håkansson continued. “In this process we try to identify and involve as many stakeholders as possible in order to fully understand the issues at the airport. Based on the outcome of this study a solution can be presented alongside an implementation plan.”
Airfield lighting’s bright future in LEDs
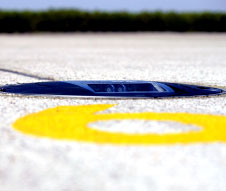
All atg products are manufactured to be compliant to International Standards requirements, and its portfolio of expertise includes Airfield Ground Lighting, Control Systems & CCR Equipment, Maintenance & Service, Planning & Airfield Surveys and the project management of global AGL works.
Airfield Ground Lighting (AGL) is an airside safety critical component which helps pilots safely land and manoeuvre around an airfield. Increasingly cutting-edge and ecological illuminating solutions are emerging onto aprons, taxiways and runways, emphasising a reduction in airport carbon emissions, as well as reduced costs, as suppliers work to provide sustainable platforms for their customers to achieve the highest environmental standards. “The traditional technology used for lighting airfields is Tungsten Halogen, however, as technical advances occur, it is now gradually being phased out in favour of the LED (Light Emitting Diode),” said Kevin Armstrong, Sales & Marketing Director, atg airports. “LEDs possess various attributes which make them suitable for use in airfield lighting circuits including increased lifetime, lower power consumption which helps reduce the airport’s carbon footprint, along with reduced maintenance requirements.”
Consistently breaking new ground in embedded airfield lighting systems, atg airports is the only UK-based specialist manufacturer and installer of AGL, and has provided solutions to 576 International Civil & Military Airfields in 107 countries over the last two decades. IRIS, atg’s market-leading range of High Intensity LED airfield lighting fittings, is setting the standard in airfield lighting. “IRIS’s state-of-the-art technology includes a number of innovative features designed to make airfield maintenance quicker and easier,” explained Armstrong. The introduction of an optical cartridge as a housing for the prism allows for the unit to be replaced quickly, providing a commonality of parts which will significantly reduce the spares holding of the airport. The ultra-low profile design of the IRIS range, which has no negative slope, helps to improve the ride comfort for airline passengers and reduce the impact on landing gear minimising any aircraft damage.
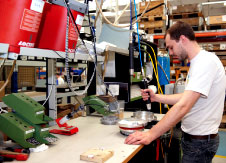
ADB Airfield Solutions tailor-makes lighting solutions to support customers’ goals of relying on more energy efficient resources or materials. “For example, one of the world’s largest international airports asked us to investigate a power supply system to maximise efficiency, eliminate internal power supply while reusing its existing series circuit infrastructure. We developed a new DC Series LED power system, which uses up to one-tenth of the energy that a traditional 6.6A incandescent circuit does,” said CEO Onselaere.
ADB Airfield Solutions, a world leader in airfield lighting, offers a comprehensive range of visual guidance solutions, including AD Lights – easy-to-maintain, environment-friendly and cost-efficient LED fixtures for various AGL applications including the taxiway and runway, touchdown zones and guard lights – and guidance signs, which provide visual directions to taxiing aircraft and airport vehicles. One of the first to begin developing the technology for an airfield environment, ADB has pioneered the use of energy efficient LEDs for airfield lighting, with over 500,000 LED solutions installed at more than 450 airports globally and its range of solutions implemented at 2,000 airports in 175 countries. The provider also offers full end-to-end services, ranging from AGL design to products and solutions, system engineering and consulting services, to help airports manage their carbon footprint by reducing power usage and address the complexity of operations.
“We expect the transition from incandescent, traditional lighting to LED to occur gradually, with airports first installing LED lighting at the most crucial areas such as taxiways and runways, and then approach. As airports upgrade and modernise their airfield lighting infrastructure, they will be cognisant of the immense benefits of LEDs both from sustainability and cost viewpoints, and migrate to LED technology,” said CEO Christian Onselaere. “Our solar solutions emphasise the use of clean, alternative energy sources to reduce carbon emissions from use of conventional power sources. Apart from enabling up to 84% energy savings (compared to incandescent lights), our LED range is low maintenance and provides greater operational efficiencies. In effect, this translates to lower labour costs, lesser vehicular movement and lower fuel costs. Our power systems offer more energy-efficient ways of distributing power to the different lights and systems,” he concluded.